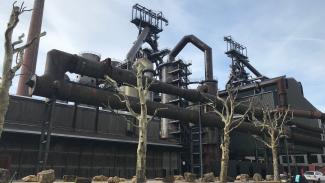
© Uwe Hentschel
Jusqu’au milieu des années 1990, trois de ces hauts fourneaux se trouvaient sur le site universitaire de Belval. Deux sont encore debout aujourd'hui.
Face à des températures pouvant atteindre 2 000 degrés Celsius, la marge de manœuvre est limitée : « Vous pouvez mesurer les flux de gaz chaud entrant et les températures dans la partie supérieure, mais cela ne vous renseigne pas sur ce qui se passe plus bas à l’intérieur des hauts fourneaux », explique Bernhard Peters. Ce professeur de thermodynamique et de dynamique des fluides, directeur de l’équipe de recherche LuXDEM de la Faculté des Sciences, de la Technologie et de la Communication (FSTC), s’est approché de très près de ce qui ne peut être mesuré.
Dans un haut fourneau, la fonte brute est produite à l’aide de la chaleur du minerai de fer, un mélange de composés chimiques de fer et de roches non ferreuses. Le four est rempli en alternance par le haut avec du minerai de fer et du coke, de sorte que des couches de ces deux composants se forment à l’intérieur. Le coke obtenu à partir du charbon sert de combustible. Il est ventilé par l’apport d’air chaud à des températures pouvant atteindre 1 300 degrés Celsius. Avec le gaz réducteur ainsi formé, les minerais de fer sont réduits et fondent en raison des températures élevées. Le fer fondu et les scories s’égouttent dans le compartiment situé dans la partie inférieure du haut fourneau. Le fer fondu est ensuite transformé.
XDEM : la simulation la plus précise que les ordinateurs peuvent actuellement effectuer
Jusqu’au milieu des années 1990, trois de ces hauts fourneaux se trouvaient sur le site universitaire de Belval. Le dernier a été fermé en 1997. Le plus grand et le plus récent, le haut fourneau C, a été démonté et vendu à la Chine ; les deux autres fours A et B sont classés monuments culturels depuis 2000. Des visites guidées sont également proposées sur le haut fourneau A depuis 2014.
Si le principe des hauts fourneaux est bien connu, nos connaissances des procédés exacts restent approximatives. C’est pourquoi Peters et son équipe ont développé XDEM (eXtended Discrete Element Method). Il s’agit d’un modèle de simulation qui permet de représenter en détail les processus dans les hauts fourneaux. « Il existe déjà des modèles simples, mais il nous reste à découvrir et définir de nombreux coefficients empiriques », explique l’ingénieur. Plus les modèles sont précis, moins ces données sont nécessaires, ajoute-t-il. « Et l’objet de mes travaux est la chose la plus précise qui puisse être faite avec la puissance de calcul actuellement disponible ».
L’ajout des bonnes quantités de coke et d’oxyde de fer est crucial pour l’optimisation des processus dans les hauts fourneaux
XDEM est intéressant à la fois pour les concepteurs et les exploitants de hauts fourneaux. « Le contrôle de l’ajout de minerai de fer et de coke a une grande influence sur le fonctionnement des fours, explique M. Peters. Si, par exemple, la température baisse dans une certaine zone du four, le fer s’égoutte plus lentement », explique le chercheur, qui compare le procédé à un tas de gravier : « Quand on verse de l’eau sur le gravier, il s’écoule rapidement. Mais si on prend du miel à la place de l’eau, la durée d’écoulement sera plus longue ».
Un haut fourneau fonctionne selon le principe du contre-courant : « Le gaz chaud monte vers le haut, tandis que le fer fondu et les scories s’égouttent vers le bas », explique l’ingénieur. Ces processus sont influencés par la température dans certaines zones du four.
Simuler des processus critiques sans avoir à les tester
« Avant l’avènement des ordinateurs, ces processus étaient purement empiriques. Lors de la conception des hauts fourneaux, nous nous sommes appuyés sur une très longue expérience, explique M. Peters. Quand les choses prenaient une mauvaise tournure, on savait comment réagir ». Avec l’aide de XDEM, de tels processus peuvent être simulés sans avoir à les tester.
« Nous pouvons donc également étudier certains scénarios de simulation et voir comment le processus est affecté lorsque nous modifions certains paramètres », explique le chercheur. Les connaissances acquises peuvent être déterminantes pour le fonctionnement du four : « Si le fer fondu et les scories ne s’égouttent pas assez rapidement, mais restent coincés sur le coke, le haut fourneau peut s’obstruer », explique M. Peters.
La prochaine étape : Confirmer la qualité du modèle de calcul
En tant qu’exploitant d’un haut fourneau, vous pouvez y remédier en réagissant rapidement dès les premiers signes. Mais il serait bien plus astucieux de simuler un tel scénario à l’avance pour que cela ne se produise jamais dans la pratique. Le développement de ce modèle de calcul jette les bases de cette nouvelle approche.
La prochaine étape pour M. Peters et son équipe consistera à travailler sur des calculs concrets pour déterminer les processus au sein d’un haut fourneau. Pour ce faire, ils utilisent les mesures d’un haut fourneau de laboratoire, qui sont comparées aux résultats des calculs afin de confirmer la qualité du modèle de calcul.
Auteur : Uwe Hentschel