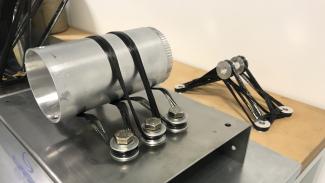
© Uwe Hentschel
Le support de ce tube semble fragile, mais il est très résistant
Le lancement d’une Golf diesel neuve dans l’espace coûterait une bonne dizaine de millions d’euros. Et si le réservoir était plein, il faudrait ajouter encore facilement 400 000 euros. Les données du LIST (Luxembourg Institute of Science and Technology), selon lesquelles il faudrait débourser entre 5000 et 10 000 euros pour chaque kilo de poids, ne sont peut-être fondées que sur des estimations approximatives, mais même sans données précises, l’équation se résume très simplement. Plus la pièce est lourde, plus le transport est coûteux.
Structure en 3D robuste à partir d’un filament tissé avec revêtement polymère
« En particulier pour le transport, les besoins en énergie sont étroitement liés au poids » explique Damien Lenoble, Directeur du département de recherche et de technologie des matériaux du LIST. C’est une autre raison pour laquelle le LIST travaille depuis déjà un certain temps sur la recherche de composants légers pour l’industrie aéronautique et aérospatiale, explique D. Lenoble. Pour lui, la coopération désormais lancée avec l’entreprise luxembourgeoise Gradel marque une autre étape importante sur cette voie. Bien sûr, cette coopération ne concerne pas le transport de voitures dans l’espace, mais par exemple de satellites (qui sont plus légers). Cependant, à l’avenir cette nouvelle technologie pourrait également être utilisée dans les industries aéronautique et automobile.
Dans un laboratoire de recherche commun sur le site du LIST à Hautcharage, les chercheurs du LIST et Gradel souhaitent se consacrer à la recherche et aux essais de structures ultra-légères mais très robustes. Des fibres de carbone sont à cet effet revêtues d’un polymère qui durcit l’ensemble de l’objet et le rend extrêmement solide et résistant. Les fibres de carbone imprégnées sont enroulées sous forme de filament pour produire une structure en maille 3D optimisée qui confère à la pièce ses propriétés mécaniques particulières.
Fabrication entièrement automatisée de composants à l’aide d’un bras robotisé
Un procédé appelé « xFKin3D » est mis en œuvre afin de créer les pièces par tissage du filament. Il n’est toutefois pas nécessaire que le support du revêtement polymère soit toujours de la fibre de carbone. Comme l’explique Claude Maack, Directeur général de Gradel, d’autres matériaux naturels peuvent également être employés, comme le lin, le basalte ou le verre.
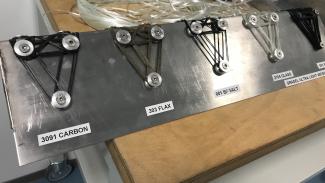
Les constructions peuvent être réalisées à partir d'une grande variété de matériaux
La collaboration entre le LIST et Gradel porte sur deux projets. Le premier vise à appliquer la technologie xFKin3D à l’espace. L’objectif est de poursuivre le développement de cette technologie afin qu’elle puisse aussi être utilisée et surtout approuvée pour la production de composants destinés à des applications spatiales.
Le second projet vise à concevoir une machine à enrouler robotisée qui permette ensuite la fabrication entièrement automatique de pièces. Un bras robotisé de Gradel déjà installé au LIST sera utilisé à cette fin. Ainsi, alors que le premier projet est plutôt de nature artisanale, l’emploi du bras robotisé doit quant à lui permettre une fabrication industrielle à plus grande échelle. Il existe déjà des clients pour cela : Thales Alenia Space et Airbus Defence and Space en France, ainsi que OHB en Allemagne, toutes trois des entreprises renommées dans le secteur des satellites.
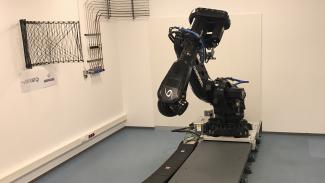
L'utilisation du bras robotisé devrait permettre une production à plus grande échelle
Réduction du poids jusqu’à 75 %
Les composants produits sont destinés à servir comme supports d’antenne ou pour la fixation d’appareils dans les satellites. Actuellement, beaucoup de ces pièces sont en métal et donc relativement lourdes. Selon C. Maack, une réduction de poids allant jusqu’à 75 % est envisageable grâce à l’emploi de cette nouvelle technologie. « L’objectif est très simple » déclare le Directeur général de Gradel : « Seulement le matériel nécessaire, complété par le facteur sécurité, et rien d’autre ».
Gradel s’occupera entre autres de la commercialisation des produits, tandis que le LIST apportera son savoir-faire dans la composition des matériaux et mènera des recherches sur les aspects essentiels à la qualité des composants. Il s’agit par exemple de la vitesse d’enroulement, de la pression ou encore de la température.
Les deux projets sont soutenus par le programme spatial national luxembourgeois LuxIMPULSE, qui vise à fournir des fonds pour aider les entreprises basées au Luxembourg à commercialiser des idées innovantes. Le programme est géré par l’Agence spatiale luxembourgeoise (LSA) en collaboration avec l’Agence spatiale européenne (ESA).
Auteur : Uwe Hentschel
Photos : Uwe Hentschel
Infobox
La société luxembourgeoise Gradel, basée à Ellange, se présente comme suit sur son site web :
GRADEL est établie au Luxembourg depuis 1965.
Elle opère deux activités : la gestion de projet de machines spéciales dédiée à l’industrie nucléaire, spatiale, et générale, et la production de sputtering targets.
Gradel conçoit et réalise des machines spéciales clef en main (équipements mécaniques automatisés) depuis plus de 50 ans.
La société commercialise des targets rotatives, targets planar, accessoires pour coater et des services d’ingénierie dans le secteur du verre.